Understanding Certificates
How We Seamlessly Connect Your Order
from Our Location to Your Project
Certificates in the (Bio) Pharmaceutical Industry
The biopharmaceutical industry adheres to numerous standards and certifications to ensure product quality and safety. Understanding these standards is crucial for maintaining compliance and building customer trust. To help you navigate these essential regulations, we provide an overview of key certifications related to our product categories, aiding you in aligning with industry standards.
Looking for our certificate portal?
Our Certificate Portal offers easy access to your product certificates, ensuring all relevant documents are readily available when you need them.
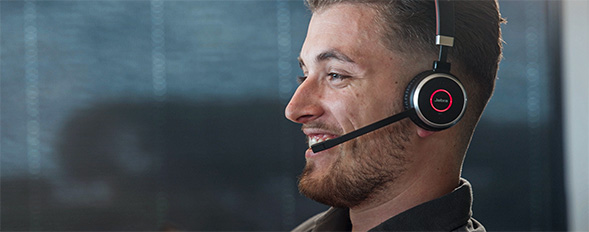
EN 1024 :2004
TYPE 2.1 DECLARATION OF COMPLIANCE
With the type 2.1 document, declaration of compliance with the order, the producer declares that the products are in accordance with the order. In this, the charge number of the products is given but neither the test report results nor chemical analysis are announced.
TYPE 2.2 TEST REPORT
With the type 2.2 document, test report document, the producer declares that the products are in accordance with the order. In the test report, the quality control test results based on non-specific inspection are given, in accordance with the general material standards. The test results are not necessarily those from the lot supplied to the customer.
Inspection certificate 3.1
Document issued by the manufacturer in which he declares that the products supplied are in compliance with the requirements of the order and in which he supplies test results.
The test unit and the tests to be carried out are defined by the product specification, the official regulation, and corresponding rules and/or the order.
The document is validated by the manufacturer’s authorized inspection representative, independent of the manufacturing department. It shall be permissible for the manufacturer to transfer on to the inspection certificate 3.1 relevant test results obtained by specific inspection on primary or incoming products he uses, provided that the manufacturer operates traceability procedures and can provide the corresponding inspection documents required.
TSE/BSE CONFIRMATION
According to the ‘Note for guidance on minimizing the risk of transmitting animal spongiform encephalopathy agents via human and veterinary medicinal products (EMEA/410/01 rev 3)’ it is necessary to ensure compliance with the requirement for the TSE/BSE safety of the used product contact equipment in the manufacture of medical products.
Therefore, producers often supply a Certificate of conformity that the materials they use do not fall under the scope of the above-mentioned guideline.
FDA
A federal agency of the United States Department of Health & Human Services is responsible for protecting and promoting public health through the regulation and supervision of among others food safety and biopharmaceutical products.
The USA Food and Drug Administration (FDA) places regulations on three different types of food additives:
Direct food additives are components added directly to the food, such as food coloring or dye.
Secondary direct food additives are components that are added as part of a treatment or process. These are substances whose functionality is required during the manufacture or processing of food and are ordinarily removed from the final food.
Indirect food additives are substances that may come into contact with food but are not intended to be added directly to food. Examples of indirect food additives are things like packing, containers, and food processing equipment.
Where does FDA 21 CFR 177 come into play in sanitary process equipment? In a word, everywhere. Every type of sanitary valve has an elastomer seal seat. Every sanitary pump has o rings associated with the seal. And of course most systems have many sanitary clamp unions with sanitary gaskets.
CFR 21 FDA 177.1550
The Federal legislation that covers indirect food additives and the most specific references to PTFE is CFR 21 FDA 177.1550, entitled “Substances for Use as Basic Components of Single and Repeated Use Food Contact Surfaces, Sec. 177.1550 Perfluorocarbon resins”.
CFR 21 FDA 177.2600
The Federal legislation that covers indirect food additives and the most specific references to rubber and rubber products is CFR 21 FDA 177.2600, entitled “rubber articles intended for repeated use”. Approved substances include acrylonitrile-butadiene copolymer (Buna), silicone, polytetrafluoroethylene, and ethylene propylene diene monomer.
USP Class VI
The U.S. Pharmacopeial Convention (USP) is a non-profit organization, to create standards for medications, food ingredients, dietary supplements, and healthcare technologies. The USP publishes biocompatibility protocols for the plastics and polymers used in medical devices or surgical equipment, that may come in contact with human tissue.
The two most common test regimens commonly used to measure biocompatibility are USP <87> and USP <88>.
To begin, USP <87> is an in vitro test designed to assess the biocompatibility of the test material in contact with a specific cell culture in a fast and sensitive way. There are three different ways this test can be carried out depending on the material tested:
- Agar diffusion
- Direct contact
- Elution
USP Class VI refers to one of the six designations for plastics from General Chapter <88> of the United States Pharmacopeia and National Formulary (USP-NF). This chapter provides guidelines for testing and certification of a material to be used within a medical device.
The USP Class VI designation is considered the most stringent and, therefore, most useful for medical applications. It involves the following three in vivo <88> biological reactivity evaluations, generally performed on mice or rabbits to mimic use in humans:
- Acute Systemic Toxicity (Systemic Injection) Test
- Intracutaneous Test
- Implantation Test
In addition to demonstrating an extremely low level of toxicity by passing these three tests, the material will be subjected to several temperature assessments for set periods of time. The standard temperatures are 50, 70 and 121 °C. Materials that meet USP Class VI standards generally ensure a high quality level and better acceptance with the FDA and USDA because the materials a believed to substantially reduce the risk of causing harm to patients from reaction to a toxic material.
USP <661> Plastic Packaging Systems and Their Materials of Construction
The purpose of USP <661> is to measure the physiochemical properties of impurities extracted from packaging for therapeutic products (pharmaceuticals, biologics, dietary supplements, and devices). The plastics used in packaging systems are composed of homologous polymers with a range of molecular weights and contain additives such as antioxidants, stabilizers, lubricants, plasticizers, colorants, and others. The extracted solution undergoes tests for identification of the material, physiochemical properties, and extractable metals.
Establishing the suitability of plastic packaging systems for therapeutic products involves multiple tests and testing procedures, as briefly outlined below:
- Material screening: Characterization of a packaging system's materials of construction to evaluate ingredients as probable extractables and potential leachables. Such a characterization facilitates the identification of materials that are suitable for use in packaging systems.
- Controlled extraction (simulation) study: Worst-case controlled extraction (simulation) study to determine the extent to which extractables may become probable leachables.
- Product assessment: Actual-case measurement of confirmed leachables in the therapeutic product in the pharmaceutical packaging/delivery system intended for the commercial market.
Additionally, information provided by the vendor(s) of plastic packaging systems and their associated materials or components of construction can facilitate suitability assessments, as such information may be appropriate additions to or surrogates for the results obtained by performing the tests noted previously.
USP <381> Elastomeric Closures for Injections
The purpose of USP <381> is to measure the physicochemical properties of impurities extracted from elastomeric closures. The extract solution is analyzed for non-volatile residue, turbidity, acidity/alkalinity, reducing substances, heavy metals, color, zinc, optical absorbance, ammonium, and volatile sulfides.
EHEDG
EHEDG, the (European Hygienic Engineering and Design Group) is a European-based non-governmental organization devoted to the advancement of hygienic design and food engineering. EHEDG is a consortium of equipment manufacturers, food industries, research institutes, and public health authorities, founded in 1989 to promote hygiene during the processing and packing of food products.
European legislation requires that handling, preparation, processing, packaging, etc.
of food is done hygienically, with hygienic machinery in hygienic premises (the food hygiene directive, the machine directive, and the food contact materials directive).
EHEDG provides practical guidance on hygienic engineering aspects, which details the principal hygienic design criteria to be met by equipment for the processing of foods. It gives guidelines on how to design, construct, and install such equipment so that it does not adversely affect food quality; especially safety. The guidelines apply to durable equipment used for batch and continuous, open, and closed manufacturing operations. As food safety does not end at the borders of Europe, the EHEDG actively promotes global harmonization of guidelines and standards.
The Pressure Equipment Directive 2014/68/EU
The Pressure Equipment Directive (PED) 2014/68/EU (formerly97/23/EC, applied up until 18.07.2016) [1] of the EU sets out the standards for the design and fabrication of pressure equipment (‘pressure equipment’ means steam boilers, pressure vessels, piping, safety valves and other components and assemblies subject to pressure loading) generally over one litre in volume and having a maximum pressure more than 0.5 bar gauge. It also sets the administrative procedures requirements for the ‘conformity assessment’ of pressure equipment, for the free placing on the European market without local legislative barriers. It has been mandatory throughout the EU since 30 May 2002, with 2014 revision fully effective as of 19 July 2016. The set out standards and regulations regarding pressure vessels and boilers safety are very close to the US standards defined by the American Society of Mechanical Engineers (ASME).
1935/2004/EC
Throughout the EU the core legislation controlling all food contact materials and articles is European Regulation (EC) number 1935/2004. This Regulation came into force on 3 December 2004 and replaced the previous ‘framework’ Directive that had been in place for fifteen years, Council Directive 89/109/EEC. The European Regulation is directly and fully applicable in all EU Member States.
The Regulation applies to all materials and articles which, in their finished state, are intended to come into contact with food, including so-called ‘active’ and ‘intelligent’ food contact materials and articles. It also brings two other types of materials or articles within the scope of the Regulation. The first are those materials and articles that can reasonably be expected to be brought into contact with foods, for example the linings inside refrigerators. The second are those that can reasonably be expected to transfer their constituents to food, for example, printing inks and adhesive labels that may be used on packaging.
ADI-Free Certificate
Animal Derived Ingredient-Free Materials
ADI-Free certification confirms that a product—typically elastomeric components like gaskets, O-rings, and valve seals—contains no animal-derived ingredients at any stage of its production. This includes raw material sourcing, manufacturing, and post-processing treatments.
Products that are ADI-Free are essential for industries that require the highest levels of material purity and safety, such as the biopharmaceutical, medical, and food processing sectors. These applications often demand materials that are free from any risk of contamination or transmission of animal-borne diseases, such as:
- Bovine Spongiform Encephalopathy (BSE)
- Transmissible Spongiform Encephalopathy (TSE)
By using ADI-Free certified materials, manufacturers can meet strict regulatory compliance and ensure product safety in critical applications.
ATEX
A potentially explosive atmosphere is composed of air mixtures of gases, vapors, mists, or dust, which can ignite under certain operating conditions.
Equipment and protective systems intended for use in potentially explosive atmospheres cover a quite large range of products, including equipment used on fixed offshore platforms, in petrochemical plants, mines, flour mills, and other areas where a potentially explosive atmosphere may be present.
The ATEX Directive 2014/34/EU relating to equipment and protective systems intended for use in potentially explosive atmospheres, has been applicable since 20 April 2016.
In this directive areas where hazardous explosive atmospheres may occur are classified into zones. The classification given to a particular zone, and its size and location depends on the likelihood of an explosive atmosphere occurring and its persistence if it does.
Areas classified into zones:
Hazard – Gas-vapor-mist
Zone 0 - A place in which an explosive atmosphere consisting of a mixture with air of dangerous substances in the form of gas, vapor, or mist is present continuously or for long periods or frequently
Zone 1 - A place in which an explosive atmosphere consisting of a mixture with air of dangerous substances in the form of gas, vapor or mist is likely to occur in normal operation occasionally.
Zone 2 - A place in which an explosive atmosphere consisting of a mixture with air of dangerous substances in the form of gas, vapor or mist is not likely to occur in normal operation but, if it does occur, will persist for a short period only.
Hazard - Dusts
Zone 20 - A place in which an explosive atmosphere in the form of a cloud of combustible dust in the air is present continuously, for long periods, or frequently.
Zone 21 - A place in which an explosive atmosphere in the form of a cloud of combustible dust in the air is likely to occur in normal operation occasionally.
Zone 22 - A place in which an explosive atmosphere in the form of a cloud of combustible dust in the air is not likely to occur in normal operation but, if it does occur, will persist for a short period only.
Equipment and protective systems intended to be used in zoned areas must meet the requirements of the directive. Zone 0 and 20 require Category 1 marked equipment, zone 1 and 21 require Category 2 marked equipment and zone 2 and 22 require Category 3 marked equipment. Zone 0 and 20 are the zones with the highest risk of an explosive atmosphere being present.
ISO 2230
Rubber Products - Guidelines for Storage
This International Standard gives guidelines for the inspection, recording procedures, packaging, and storage of products, assemblies, and components made from vulcanized or thermoplastic rubber prior to being put into circulation.
It applies to both solid and cellular rubber products prepared from dry raw rubber, latex, or other sources. It is not intended for use with raw rubber in bale, liquid (solution or emulsion), or particulate form, storage guidance for which is given in ISO 7664.
The recommendations for packaging form an integral part of the controlled storage procedure, as well as providing means of identifying the material and product.
Recommended shelf-life:
Group | Initial Storage Period | Extension storage periods |
---|---|---|
A | 5 YEARS | 2 YEARS |
B | 7 YEARS | 3 YEARS |
C | 10 YEARS | 5 YEARS |
Group A: a.o. BR
Group B: a.o. NBR, IIR
Group C: a.o. EPDM, FKM