ROMYNOX Cleanroom
Welcome to Our ISO 7 Class C Cleanroom: Where Excellence Meets Compliance
At ROMYNOX, we take immense pride in our unwavering commitment to quality, precision, and regulatory compliance in the biopharmaceutical industry.
Our cutting-edge ISO 7 Class C cleanroom is the cornerstone of our operations, meticulously aligned with ISO.
The Gold Standard in Cleanroom Technology
Our ISO 7 Class C cleanroom represents the pinnacle of controlled environments. It is meticulously designed and maintained to adhere to the most stringent regulations and standards.
This ensures that our cleanroom is an oasis of purity where we assemble single-use sets vital to the biopharmaceutical industry.
What Sets Our Cleanroom Apart
- Our cleanroom operates in strict accordance with ISO 14644-1:2015 for air cleanliness, ensuring the highest levels of safety and product quality.
- Advanced Airflow Control: Our state-of-the-art airflow management Lighthouse system maintain precise air quality control, effectively reducing the risk of contamination and safeguarding the integrity of your products.
- Stringent Quality Control: We employ rigorous quality control protocols at every stage of assembly, guaranteeing that our single-use sets meet and exceed industry expectations.
- Trained Professionals: Our dedicated team of experts is extensively trained in GMP compliance, ISO standards, and cleanroom protocols, ensuring that every product assembled meets the highest standards.
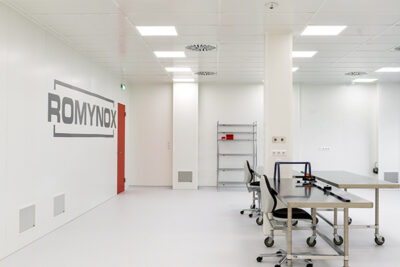
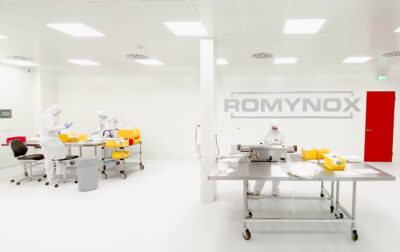
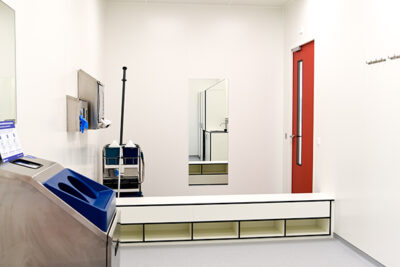
Our Commitment to Biopharmaceutical Excellence
ROMYNOX is steadfast in our commitment to delivering single-use sets that contribute to the success of the biopharmaceutical industry.
Our ISO 7 Class C cleanroom stands as a testament to our dedication to quality, regulatory compliance, and innovation.
Explore Our Cleanroom
Discover the technology and expertise that power our cleanroom operations.
Explore our website to learn more about our facility, quality assurance processes, and the diverse range of single-use sets we offer.
Contact us today to discuss your specific biopharmaceutical needs and let us demonstrate how our commitment to excellence can elevate your projects.
Join us in setting the highest standards in biopharmaceutical manufacturing – where precision, compliance, and quality converge.
if you want to visit us for an audit or want a live tour through a remote assistance inspection solution, please contact us at info@romynox.nl
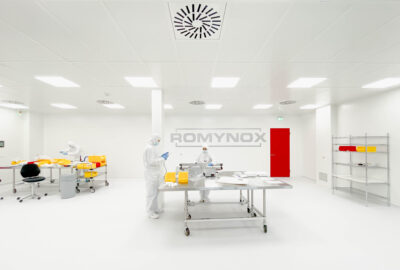